Products Details
The drying furnace is mainly used in mineral processing, building materials, metallurgy, chemical industry and other departments to dry materials with a certain humidity or particle size. It is a commonly used mining machinery and equipment. The drying furnace is reliable in operation, flexible in operation, strong in adaptability, and large in processing capacity. The drying furnace can also be called a rotary drum drying furnace. Both ends of the drying furnace host are highly sealed, which is energy-saving and environmentally friendly. The wet material is sent to the hopper by the belt conveyor or bucket elevator, and then enters the feeding end through the feeding pipe of the feeding machine of the hopper. The inclination of the feeding pipe should be greater than the natural inclination of the material so that the material can flow into the drying furnace smoothly. The cylinder of the drying furnace is a rotating cylinder that is slightly inclined to the horizontal line. Materials are fed from the higher end. The heat carrier enters from the lower end and contacts the material in countercurrent, and some heat carriers and materials flow into the cylinder together. With the rotation of the cylinder, the material moves to the lower end under the action of gravity. When the wet material moves forward in the barrel, it receives heat from the heat carrier directly or indirectly, so that the wet material can be dried, and then it is sent out at the discharge end through a belt conveyor or a screw conveyor. The inner wall of barrel is equipped with lifting flight, which can lift the materials and scatter them, increases contact surface of materials and airflow, in order to improve the drying speed and forward the materials advancement. The heat carrier is generally divided into hot air, flue gas, etc. After the heat carrier passes through the drying furnace, a cyclone dust collector is generally required to capture the material in the gas. If you need to further reduce the dust load of the end gas, it should pass through the bag filter or wet dust collector and then be released. Drying furnace equipment has many advantages, its performance is stable and good, energy consumption is relatively low, and it can be used in a wide range. The drying area of the drying furnace is divided into several. Multiple drying areas not only increase the drying power, but also save energy and reduce consumption. In addition, the performance of the drying oven is much stronger than that of the traditional dryer, the performance is more stable, the operation is easier, and the drying time is shorter, which is why the drying oven is so widely used.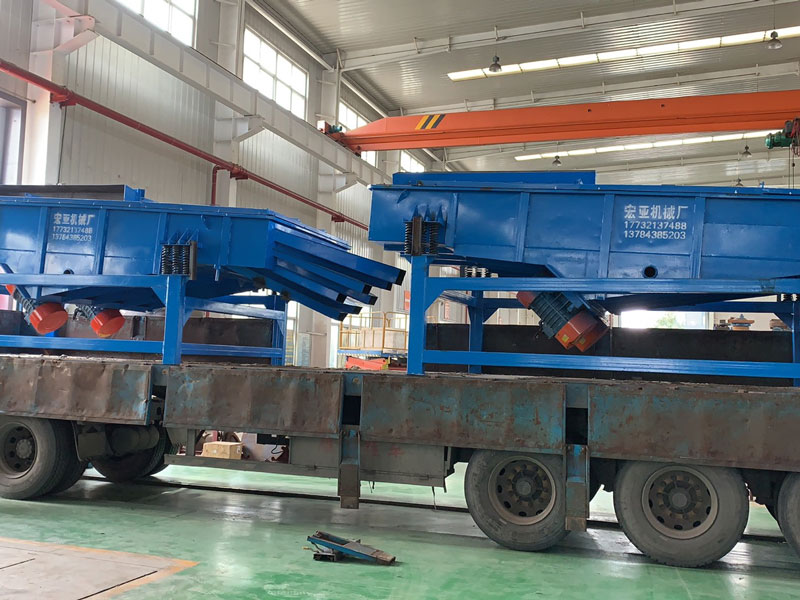
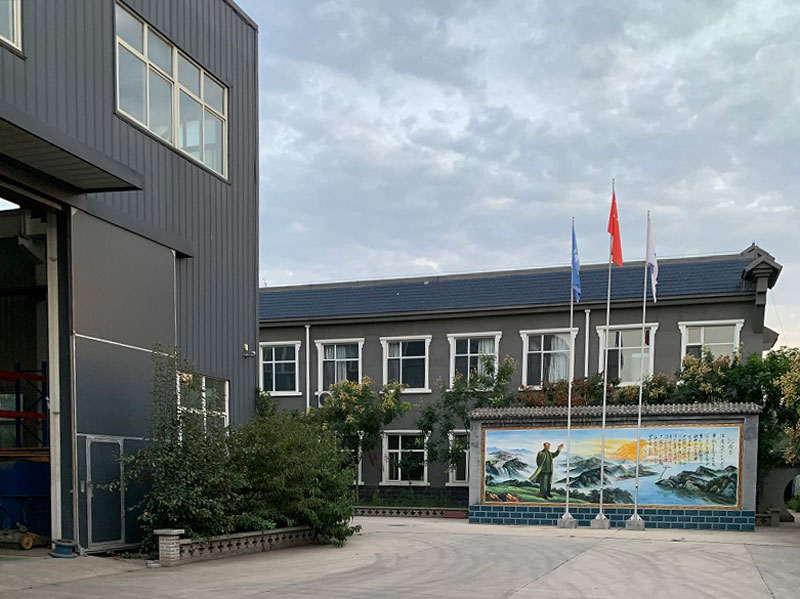
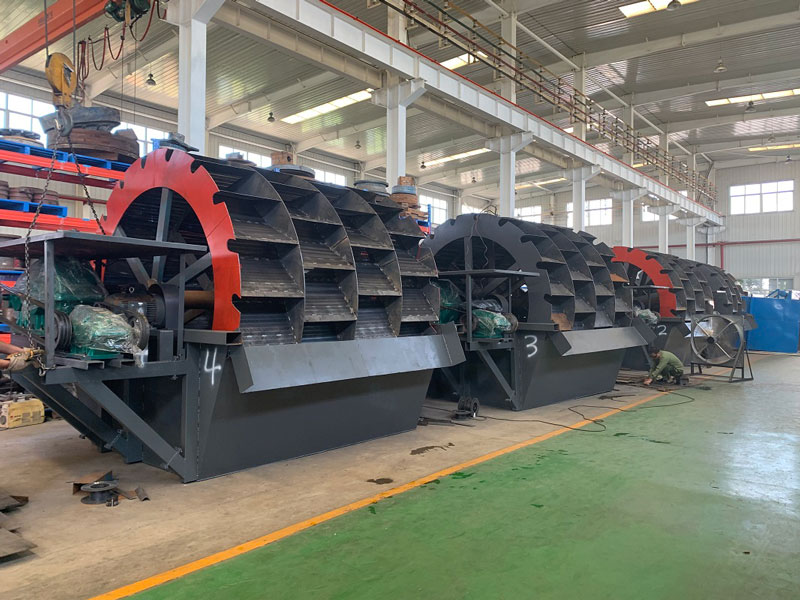
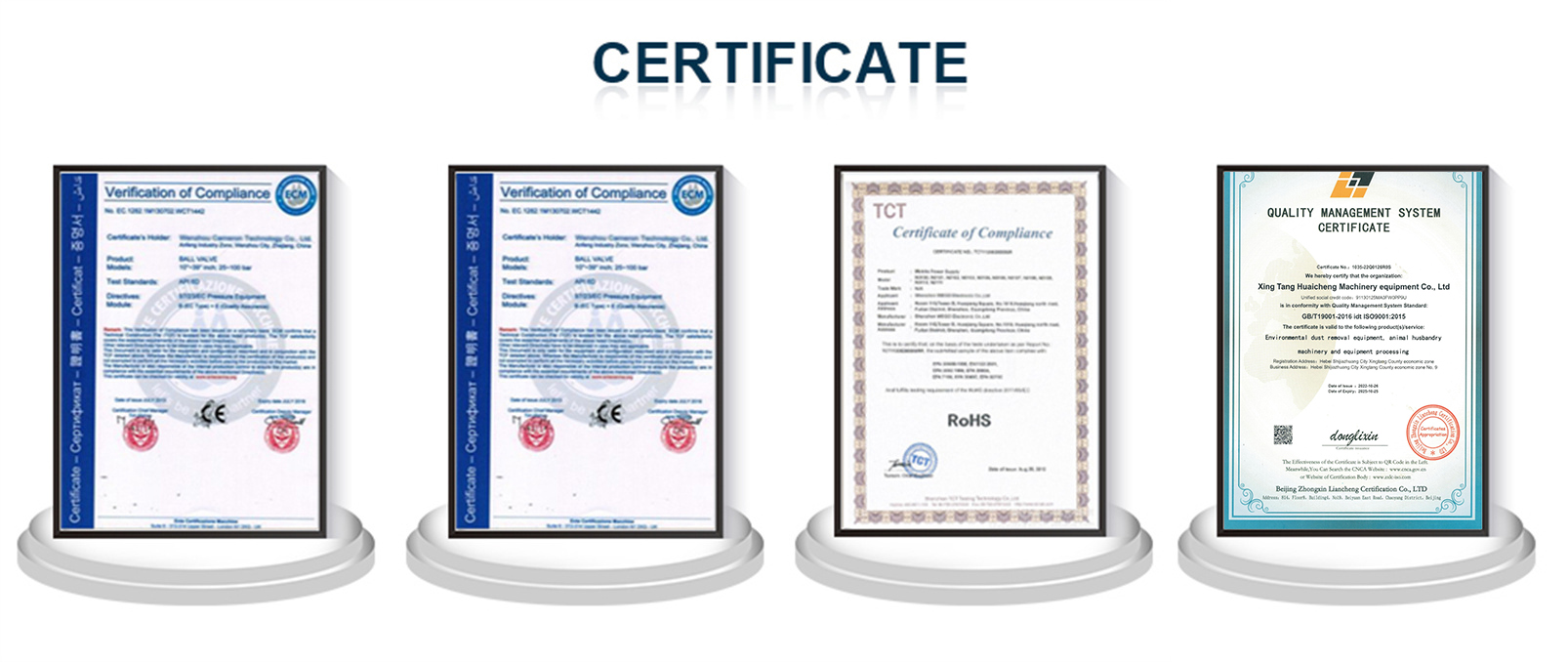
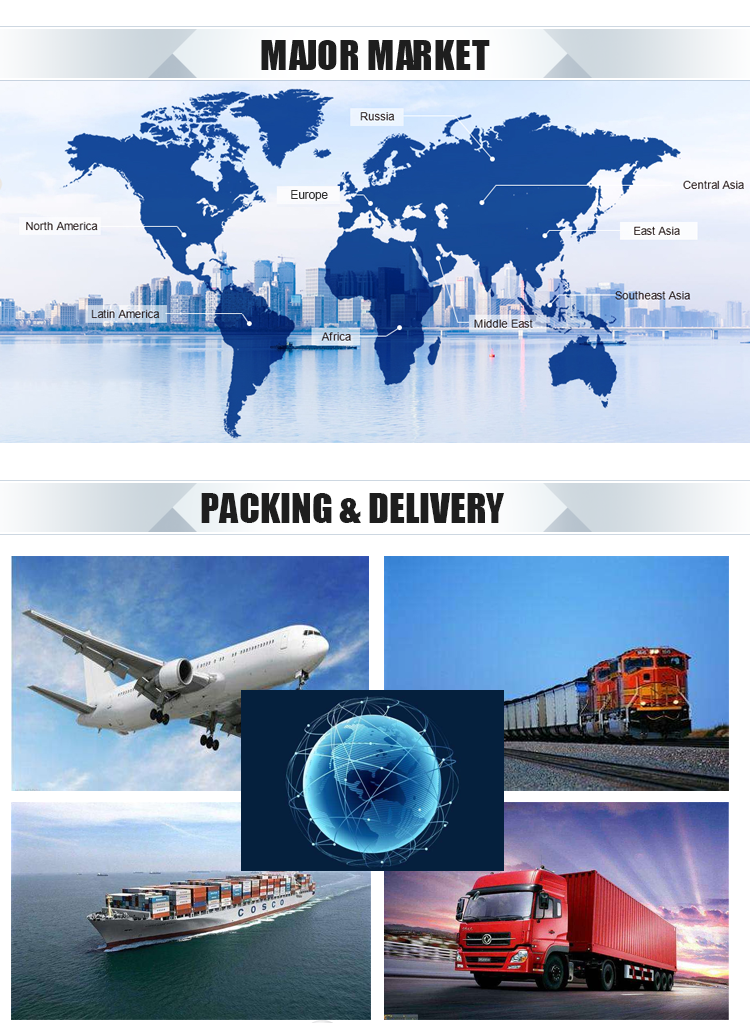
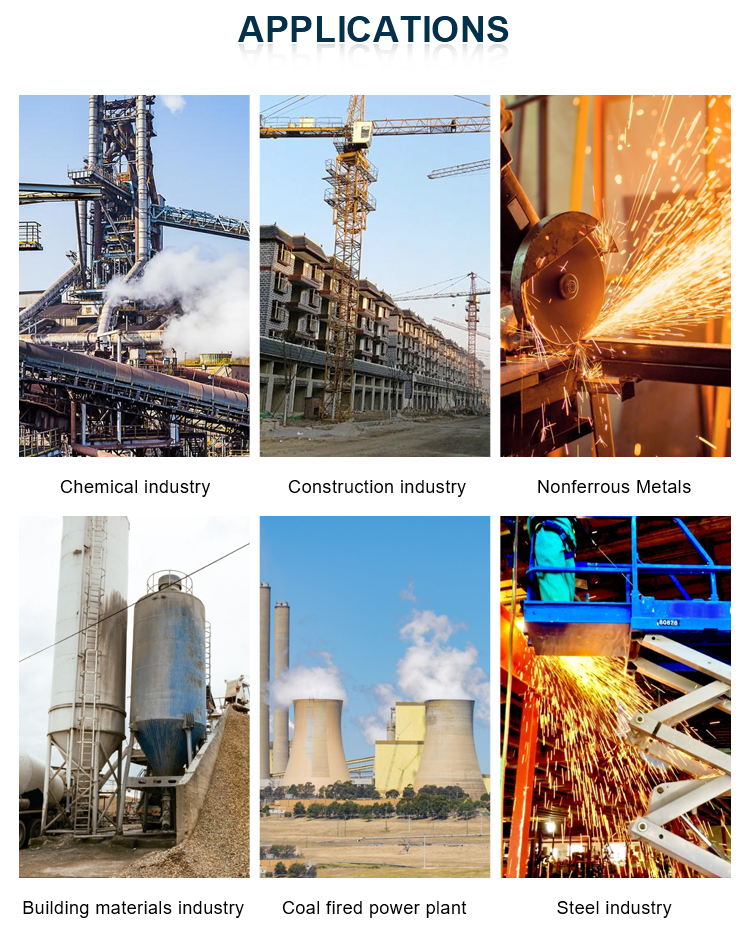
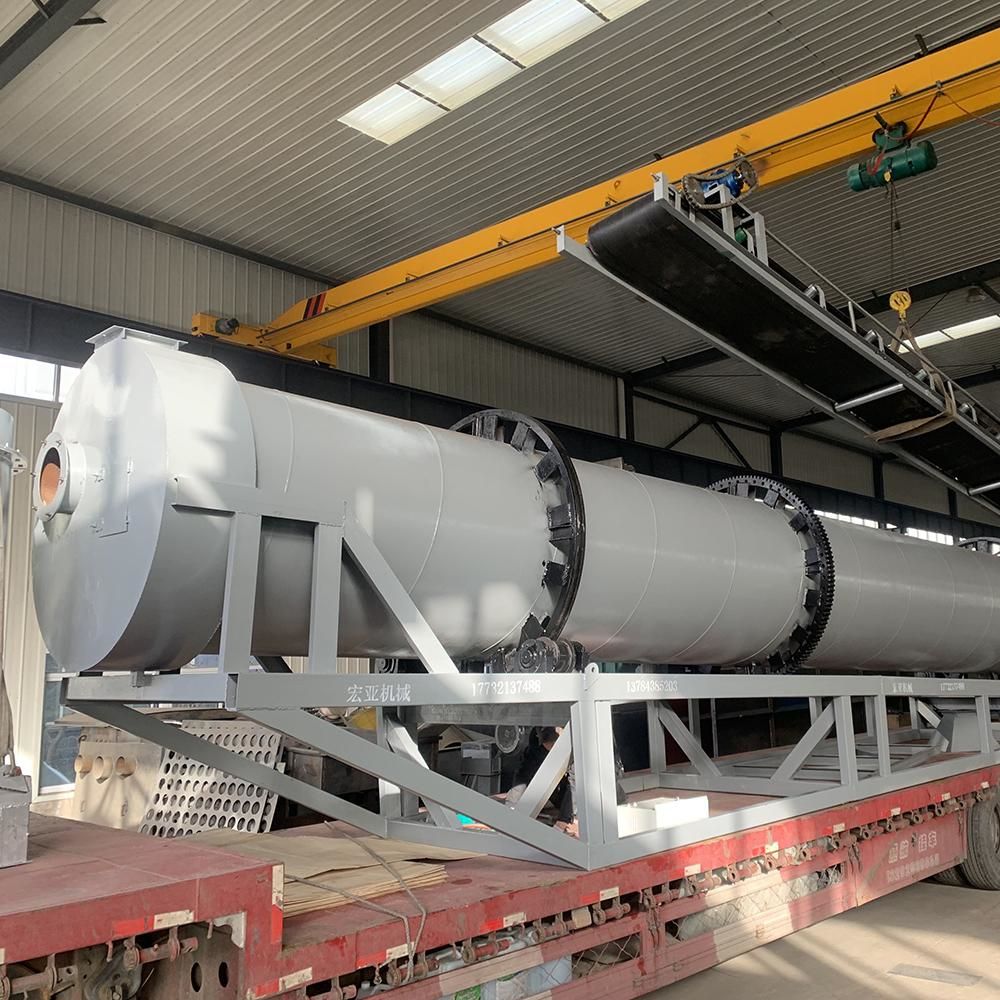
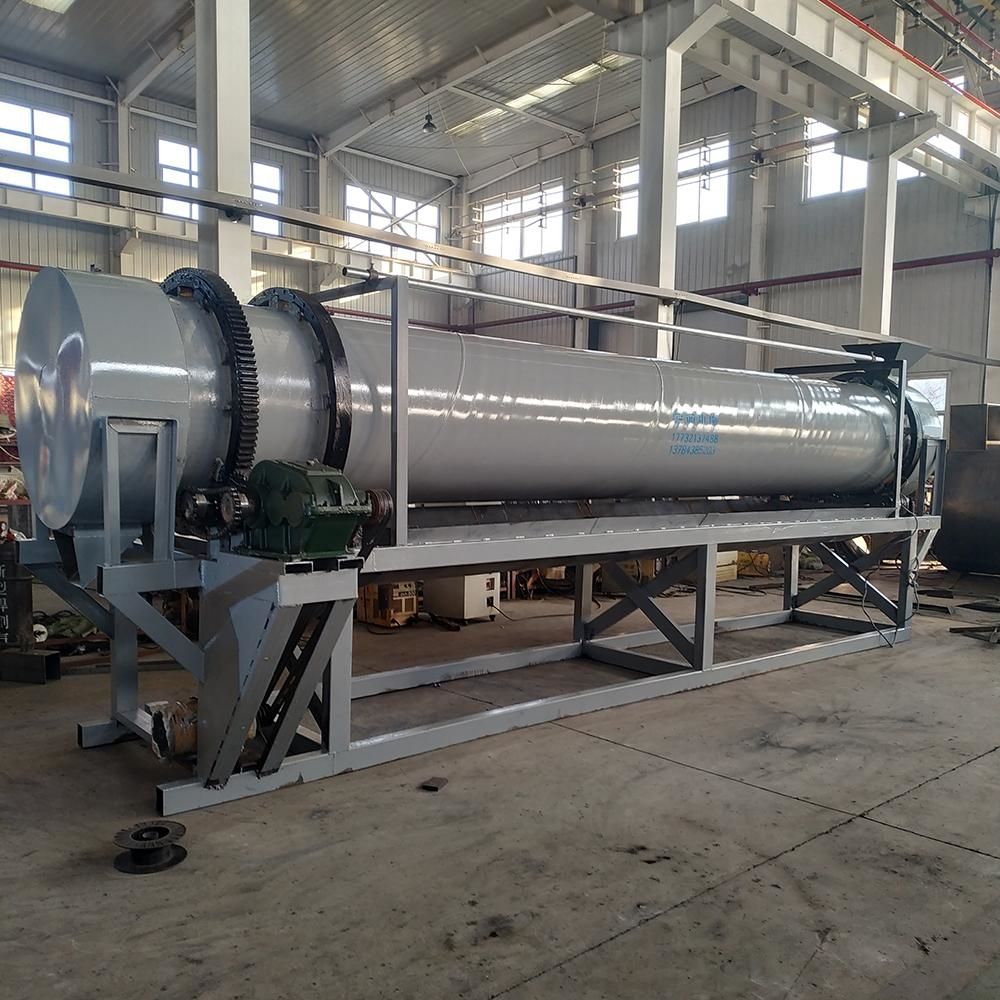
Example 1: After the coal in this coal factory is dried by the rotary drying furnace, the fly ash is absorbed by the dust collector, and the dried material is discharged from the lower outlet, and the dried product is transported to the designated position by the conveyor.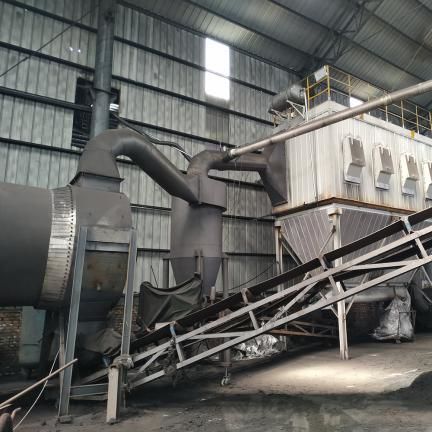
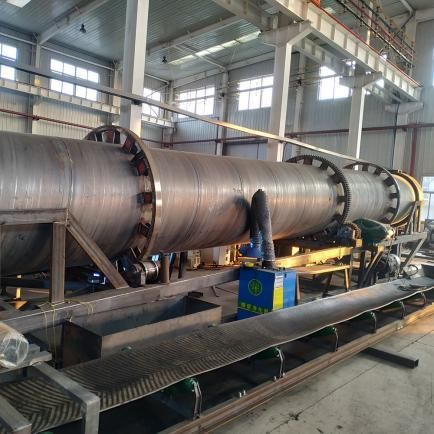
Example 2: This is the supporting facility of the sand factory. After the sand is washed by the sand washing machine, it is screened. However, the surface moisture of the material is very large, and it needs to be dried in a rotary drying furnace.
Manure Dropping Spreader,
farm fertilizer machine,
Dhan Jharne Wala Machine,
Dust Collector,
Material Handling Equipment,
Silage Loaders,
Screen Machine,
Air Filter Dust Collector,
Dust Suppression Fog Cannon,
Vibrating Screen Filter,